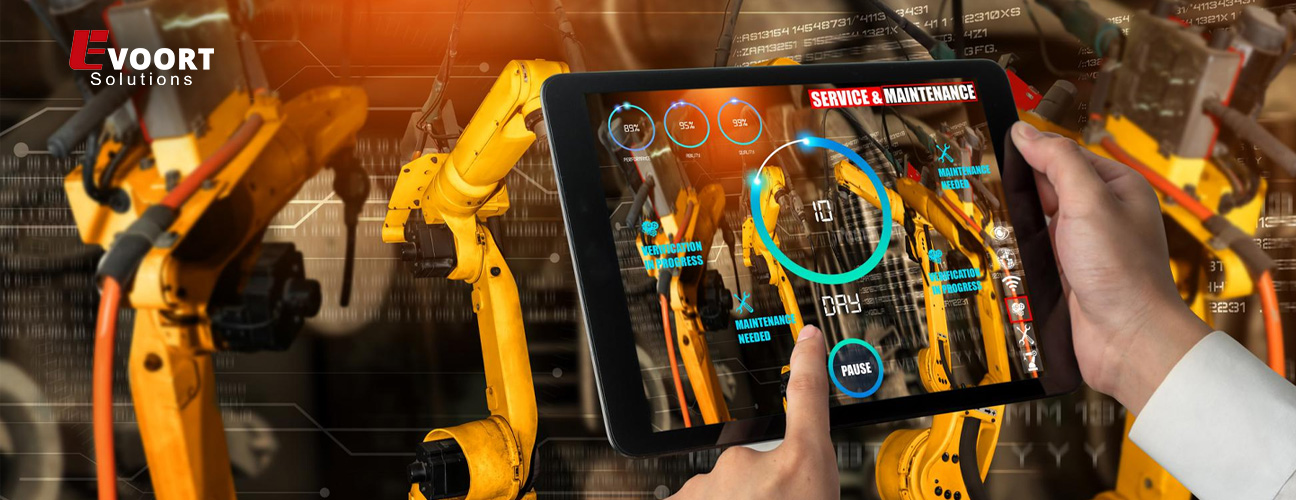
How Predictive Maintenance Moves Forward the Manufacturing Industry
Table of Contents
Equipment outage not only decreases production but also has an impact on ROI in your production plant. Any unexpected stoppage can result in setbacks such as higher repair costs, supply shortages, and lower value in the manufacturing plant. It also has a detrimental influence on OEE (Overall Equipment Effectiveness). Predictive maintenance and digital transformation solutions, thankfully, come in handy. Well with aid of the predictive maintenance approach, the manufacturing sector may enhance OEE, minimize operational costs, and reducing operational bottlenecks. This idea is critical in modern business processes. Let us look at how predictive maintenance boosts a machine's ROI over time. But first, we will look at how this notion operates in the industrial industry.
Predictive Maintenance:
What It Is and How It Helps in the Manufacturing Sector Predictive Maintenance is a strategy for identifying abnormalities in various operations and potential equipment flaws so that they may be fixed before they cause harm to the machinery. This technology predicts potential problems by utilizing data analytics tools and methodologies. Simply, predictive maintenance allows companies to save money. The predictive maintenance approach incorporates condition-monitoring tools for tracking the functioning of any piece of equipment under idle, standard, and peak circumstances. The information gathered from machinery running at varying levels of quality can assist manufacturers in planning for maintenance in advance to avoid downtime or failure.
Sensors can collect physical factors such as vibration, pressure, and temperature in actual environments, as well as chemical parameters such as the chemical amount and fluid pressure. This input would be sent to the Cloud, where AI/ML-powered algorithms will evaluate and integrate it to forecast future machine maintenance issues.
Advantages of Predictive Maintenance in Manufacturing
Rather doing scheduled maintenance and repairs on equipment at periodic intervals, it is preferable to eliminate equipment failure and discover the behaviors that cause downtime to ensure operational efficiency on the production floor. With equipment maintenance, it can lower total TCO (Total Cost of Ownership). Predictive maintenance is useful in digital process management and deployment. Predictive Maintenance's Significance in Manufacturing Predictive maintenance is to determine the optimal period to do maintenance on an asset such that maintenance periodicity is as minimal as feasible while dependability is as good as possible without incurring needless expenditures.
Predictive maintenance is particularly beneficial in situations when people are unable to act and analyze information on shop floors. Condition-based monitoring and business IoT solutions can help you gain valuable insights based on real-time data for every equipment activity.
To Recap: The industrial industry is rapidly expanding. It provides several chances and difficulties. Manufacturers can remain forefront of the competitors by seizing possibilities enabled by digital transformation solutions. Predictive maintenance has the potential to boost performance and ROI in your manufacturing firm.The benefits of investing in predictive maintenance are too big to ignore, from decreasing unplanned downtime to producing substantial cost savings and improved productivity throughout the assembly line.