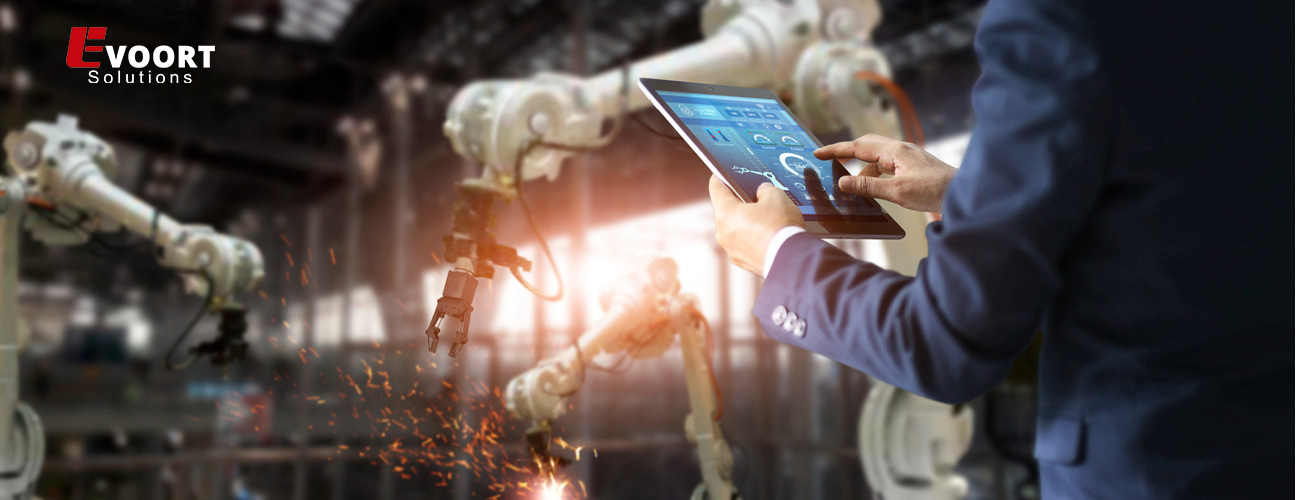
Transforming manufacturing operations to increase production speed with remote assistance
Table of Contents
Business leadership seeks to reduce overhead expenses by reducing the headcount of technical support employees at their production plant(s), while also increasing operational efficiency. This appears to be a contradiction. Is it feasible? Certainly. Because once the plant's on-site engineering support workforce has been reduced to a skeleton crew, management should seriously consider augmenting the lean production support mechanism to maintain optimum operational effectiveness and deliver output targets. Plant managers and techs have a lot on their plates: not only are they in charge of ensuring that day-to-day process runs smoothly but they are also entrusted with increasing output and income. Plant managers cannot be always around. But, in many aspects, they must be. Manufacturing plants nowadays are more efficient than ever before, frequently working continuously.
That means someone must always keep an eye on them, including while they are at their child's evening sporting event, when they are holidaying on the weekend, and even when they are asleep. Many manufacturers are finding it challenging to employ professionals in the numbers and skill sets required due to the industrial skills gap. Some organizations simply do not have access to qualified specialists within their businesses. Fortunately, there is assistance available for plant managers that offers important knowledge, backup, and support — whenever required.
Remote Assistance: A Perfect Solution
Why put off contacting your supplier or system integrator? Why leave things to chance when you can get the services of professional technicians and engineers? Remote assistance does exactly that: it gives dependable assistance for swiftly detecting problems and troubleshooting remedies in real-time. The advantages of having that remote assistance at your fingertips include increased production output, increased resolution efficiency, and increased competence to oversee operations. Remote assistance services can assist you in optimizing control system efficiency, increasing Overall Equipment Effectiveness (OEE), and lowering maintenance costs.
Remote Assistance includes the opportunity to:
- • Improve customer experience by accelerating manufacturing with fewer throughput dips.
- • Remote interaction and advice can help you optimize the precision and reliability of your work.
- • Increase judgment call speed by having plant personnel showcase planned work in real-time, allowing distant stakeholders to rapidly comprehend, agree on, and approve the job.
- • Increase the frequency of inspections as well as the documentation of work and inspections for auditing and compliance.
- • Improve employee health and safety by eliminating travel and minimizing physical contact.
- • Hands-on completion of task work with remote expert help augmented by mixed reality 3D annotations, including real-time or recorded observation for future training purposes, improves knowledge acquisition, retention, and sharing.